Haver&Boecker
Tradition and Progress of wire weaving
|
The ability to expertly weave stainless steel wire for screen printing's closest tolerance results from a long experience. Founded in 1887, Haver & Boecker has more than a century of weaving experience — and a history of intensive research and development. As early as 1902, Haver & Boecker was already weaving wire cloth in mesh counts as fine as 250. In the 1950's follows the invention of a process that revolutionized the stainless steel screen. This process was the calendering of wire screen mesh to provide unprecedented ink deposit control. Today Haver & Boek-ker offers a wide range of calendered wire mesh. Based in Hohenlimburg during its first ten years. Haver & Boecker relocated to its present site in Oelde, which appropriately neighbours the "Ruhr Area".
Throughout its history, Haver & Boek-ker's manufacturing process has consistently surpassed international quality standards (ISO 9000-9004 and 9044-9045). With input from screen printers around the world, our research team has developed measuring methods and test procedures
to perfect each phase of production. Our tight tolerances, from the selection of the wire to the final inspection of each roll we deliver, guarantee reliability. So you can count on the integrity of the wire diameter, aperture width and cloth thickness.
|
|
|
Printing with stainless steel wire cloth
|
Highly accurate registration, precision ink deposit control and high abrasion resistance top the list of benefits prompting printers to choose stainless steel wire cloth. Haver wire cloth is known for its excellent dimensional stability, and the narrow tolerance of its overall fabric thickness which provides uniform and accurate aperture widths. Haver & Boeckers technology and the nature of stainless steel itself, versus synthetics like polyester and nylon, make these benefits possible. For example, stainless steel's strength, which allows thinner wire diameters to be used.
Unlike synthetic screen fabrics, Haver Wire Cloth will not absorb moisture, and is unaffected by temperature. It virtually won't shrink, stretch or sag. It is dimensional stable, yet elastic enough, so you can stretch a highly-tensioned, drum-tight screen and print with a minimum off-contact distance. Thus assuring you the most accurate and consistent printing results.
The dimensional stability of Haver Wire Cloth also means faster set-up. Once you have stretched the screen, you go to press without undue delay.
Other important benefits of Haver Wire Cloth regard ink flow, Stensol adhesion and durability.
In any given mesh count, the open areas of wire cloth are large due to the thin wire diameters used. Thus allowing a generous ink flow. Even viscous inks flow readily, without clogging.
While synthetic fibers are slick, Wire cloth's inherently rough surface provides a good bond for your photo-Stensol. Thus producing a durable stencil.
You can expect extended service from your Haver Wire Cloth screen, because stainless steel is especially corrosion resistant and less affected by the mechanical stress of the stretching and printing processes.
Defined ink deposits can be achieved easily with Haver Wire Cloth's many available mesh options. Within any given mesh count of "as-woven" wire, there is a wide range of wire diameters. In addition, any of these can be calendered "CT Foil". Therefore your mesh choices are almost endless.
|
|
TECHNICAL DATA - HAVER WIRE CLOTH |
|
Applications for Haver Wire Cloth |
The combination of these benefits make Haver Wire Cloth perfect for applications where registration, controlled ink deposits and colour uniformity are critical. And for the most demanding applications and finest detail, there is our CT Foil, calendered, mesh. Ideal applications include:
—Printed circuit boards
— Etch mask
— Electroplated mask
—Solder mask
—Strippable lamination sheet
—Nomenclatures
—Thick film technology
—SMD technology
— Key pads
— Scales/Dash boards
—Liquid crystal displays
—Ceramics including wall tiles
—Glass bottles and hollow glassware (especially with metal-oxide inks where the wire screen acts as an electric resistor and liquifies the solid inks.)
|
|
Types of weave |
Whether you choose an as-woven or CT Foil calendered mesh, you also have the option of the following two types of weave:
Plain weave (ISO 9045)
Weave in which every warp wire crosses alternately above and below every weft wire and vice versa. Plain weave is the popular choice for screen printing due to its tight surface, wide mesh openings and ability to reproduce fine detail.
Twilled weave (ISO 9045)
Weave in which every warp wire crosses alternately above and below every second weft wire and vice versa.
Twilled weave fabrics can be woven with heavier thread diameters for a stronger mesh. They can also provide heavier ink deposits because they have greater overall fabric thickness than plain weave fabrics.
|
|
HaverWireCloth made from stainless steel |
Seen through a microscope, the surface of the stainless steel wires appears rough. This is because during the wire manufacturing process, they are drawn through a series of diamonds in order to set the wire diameter. Then, to prevent brittleness and make the wire more elastic, it is heated to more than 1832 ° Fahrenheit (1000 °C) and cooled slowly in a controlled process. |
|
Wire diameter & tolerances |
By drawing the stainless steel wires through a descending of smaller and smaller-sized diamonds, very narrow diameters can be produced that are accurate within 1 micron.
The pinpoint precision of the diamonds makes this close tolerance possible, along with the fact that this is a coldform process that does not generate enough heat to swell or melt the stainless steel.
Available stainless steel wire diameters range from 0.0007" to 0.0055".
When a thinner wire diameter is used to produce the same mesh count, the screen surface has a larger percentage of open area, which produces a heavier ink deposit (refer to the "Ultra Thin" section of the Technical Data Table).
|
|
Stretching
conduct
|
The diagram of tensioning demonstrates the stretching conduct of several materials. The synthetic mesh curves illustrate that the off-contact distance with these materials has to be much higher than with Haver Wire Cloth. Within the recommended tensions, Haver Wire Cloth has an enlon-gation of about 0,5%, whereas polyester fabrics elongate about 1,5% to 2,5% and polyamid (nylon) fabrics about 5% to 6%. |
This graph shows the load-elongation curves of various screen fabrics compared with that of Haver Wire Cloth and an individual stainless steel wire (Haver Wire Cloth quality, load x 100). All test samples were 0.04" wide, 4" long, with 250 wires per inch and a 0.0016" wire diameter.
|
|
Mesh stability |
The use of stainless steel assures excellent dimensional stability. Even if the wire cloth is fixed at an angle to the stencil frame, the mesh keeps its rectangular form and the wire diameter does not change by parallelogram displacement. |
|
Electrostatic charge |
Haver Wire Cloth does not emit an electrostatic charge. |
|
Moisture absorption and temperature |
Stainless steel wires do not absorb moisture so Haver Wire Cloth's performance is not adversely affected by applied temperatures up to a maximum of 600 °C (1,112 ° Fahrenheit). |
|
|
Cleaning |
After weaving, each finished roll of Haver Wire Cloth is vapour degrea-sed and cleaned in an ultrasonic bath using a special process we developed. This process does not change the physical properties of Haver Wire Cloth. |
|
Theoretical ink deposit |
The theoretical ink deposit is an approximate value used to help select the most appropriate mesh count for the printing application. As seen in the diagram on the right side the ink is forced through the wire cloth in cubes, whose volume is determined by the mesh aperture (w) and the cloth thickness (d). The cubes then flow together to form an even wet ink film of theoretical thickness (0} on the substrate.
Since stainless steel wire cloth can be made with extremely thin wire diameters, it can deposit ink cubes with very small gaps between them. Therefore the ink cubes have only a small distance to flow to form a uniform ink deposit and print definition with only the most minimal serration.
In addition to the wire cloth, other factors influencing the ultimate ink deposit include: ink viscosity, surface characteristics of the substrate, photo-stencil thickness and the squeegee speed, angle and durometer.
The theoretical ink deposit (Vm) can be calculated in cm3 per m2 of wire cloth using the following formula:
|
|
Stretching Haver Wire Cloth |
To obtain the uniform tension necessary for high-quality prints, it is essential to use a stretching device that stretches in both the warp and
weft direction. Also, the frame itself must be strong enough to support the appropriate tension before and throughout printing.
|
|
Tension levels |
The listed maximum tension levels should not be exceeded when stretching Haver Wire Cloth so as not to surpass its elastic reserve, which is necessary to accomodate off-contact printing. Not exceeding the maximum recommendation is especially important when stretching the finer mesh counts with thinner wire diameters. The maximum tension levels provided (see column 14 of the technical list on page 3) include a stretching reserve of 10 %. Please note that the maximum levels exceeding 35 N/cm are theoretical in nature because such elevated tension is seldom used.
When Haver Wire Cloth is stretched within its elastic reserve, it shows no sign of fatigue, whereas the tension and elasticity of synthetic mesh
decreases continually during the printing process.
A value (in N/cm or Lbs./inch) for the maximum permissible load per unit length of the stretched wire cloth (S perm.) can be calculated by using the following formula:
In the above formula, Re(wire) represents the tensile strength of the stainless steel wire, which equals 450 N/cm2. This tensile strength has a reserve of 10 %. Again, the tension values calculated by this formula that exceed 35 N/cm are more theoretical than practical figures.
|
|
Calendering -
CT Foil
|
In the early 1950's, having realized the screen printer's need for defined ink deposits, we invented the calendering of stainless steel wire cloth for screen printing. With the protection of German, French and British patents obtained in 1956, we perfected the process to allow the maximum calendering available. Today we offer all possible options.
Our calendering process uses two steel rollers to reduce the wire mesh to a predetermined thickness without altering the wire diameter and mesh openings. The final thickness is accurate to within +/- 3 microns (0.12 mil).
Calendering removes the air pockets present in all as-woven wire mesh, which forces the wire knuckles into their final, stabilized positions. So you can acquire a stabilized screen very quickly. There is, essentially, no mesh elongation and much less need for re-tensioning.
|
|
Benefits |
Unrivaled ink deposit control tops the list of the many benefits Haver CT Foil calendered wire mesh provides. Our extensive micro-incremental calendering options let you print the exacting deposit thickness your application demands. Within any given mesh count, CT Foil is available in an unmatched selection of overall fabric thickness.
Within the faster stabilization CT Foil delivers, you can expect your production speeds to increase substantially. You will also maximize your registration capabilities due to CT Foil's increased dimensional stability. Elongation on press is virtually eliminated.
Our calendering process gives the mesh a more uniform, tighter overall fabric thickness tolerance. Therefore minimizing the ink deposit variance from print to print and run to run. In addition, the ink deposit will be uniform throughout any given print. You can also expect reducted squeegee wear because the calendered wire cloth has a smoother surface.
Current applications benefitting from the expert ink control of CT Foil mesh include: printed circuits, thick film technology, solder paste (SMD), high-tech graphics such as keypads and control panels, and printing with precious metals.
|
|
Maximum and minimum calendering |
A wide range of calendering options can be chosen, from feather rolling (minimum calendering) to a maximum calendering of 30%. Haver CT Foil can be calendered in full rolls (widths up to 49") of 50 to 100 feet.
When choosing maximum calendering, 30% of the wire cloth is compressed, resulting in an overall fabric thickness that is 70 % of two times the nominal wire diameter. To determine the overall fabric thickness of a maximum calendered CT Foil, double the nominal wire diameter you have chosen and then subtract 30%.
"Feather rolling" is what we term our minimum calendering. Only the air pockets are removed in this process, resulting in a fabric thickness that is double the nominal wire diameter of your chosen mesh. When ordering CT Foil mesh, simply specify the final overall fabric thickness you require (+/- 4 microns or 0.16 mm).
|
|
Quality assurance |
Mesh aperture accuracy is essential to exact reproduction because an extreme deviation from the nominal mesh opening can cause uneven ink deposits.
To ensure the high accuracy of Haver Wire Cloth, the mesh openings are checked by a computerized mesh measuring device. This system can measure and analyze 100,000 openings in a very short time while providing a computer printout of the results. Aperture widths from a few microns up to 250 millimeters can be measured with an accuracy up to three-quarters of a micron.
|
|
Printing geometry |
As can be seen in the following diagram, the lower the off-contact distance (a) and the greater the length of distance (f) between squeegee and Stensol frame, the lower the stress of the wire cloth, translating into longer mesh life. A minimum off-contact distance also means better registration.
Another relationship affecting the life of the mesh, Stensol and squeegee, is the size of the screen and the image area. The larger the screen frame in relation to the image area, the less stress is produced. The best results are achieved when the squeegee runs over 50 to 60% lengthwise and crosswise of the stencil frame's width (I.D.).
In order to print even the finest definition, the best results are obtained
when the wire cloth is fixed on the frame so that the wires run at an angle of 20 to 25 degrees to one side of the frame. Thus the wires are less likely to run parallel and interfere with the horizontal and/or vertical lines of the stencil.
In addition, this set-up reduces the stress on the individual wires because the squeegee crosses the wires at an angle, rather directly.
When printing multi-colour halftones, there are two means to avoid moire. One is to stretch each of the screens with the mesh at a different angle to the frame. The other is to angle the stencil differently on each screen.
Stressing of Haver Wire Cloth during squeegee movement (off-contact distance is exaggerated).
|
|
Glossary of technical abbreviations |
Aperture width, w: Distance between two adjacent warp or weft wires, measured in the projected plane at the mid-positions.
Wire diameter, d: Diameter of the wire in the woven cloth.
Number of apertures per unit length, n: Number of apertures which are counted in a row one behind the other on a given unit length. The unit length may be 1 cm, 1 dm or any other unit of length.
Pitch, p: Distance between the middle point of two adjacent wires. Nominally the sum of the aperture width w and the wire diameter d.
Vth: Theoretical ink deposit in
D: Wire cloth thickness
perm.: Permissible tension in N/cm
Re(wire): Tensile strength, material parameter
|
|
Related international standards |
ISO 9000 Quality management and quality assurance standards — Guidelines for selection and use
ISO 9001 Quality systems — Model for quality assurance in design/development, production, installation and servicing
ISO 9002 Quality systems — Model for quality assurance in production and installation
ISO 9003 Quality systems - Model for quality assurance in final inspection and test
ISO 9004 Quality management and quality system elements — Guidelines
ISO 9044 Industrial woven wire cloth —Technical requirements and testing
ISO 9045 Industrial screens and screening — Vocabulary
|
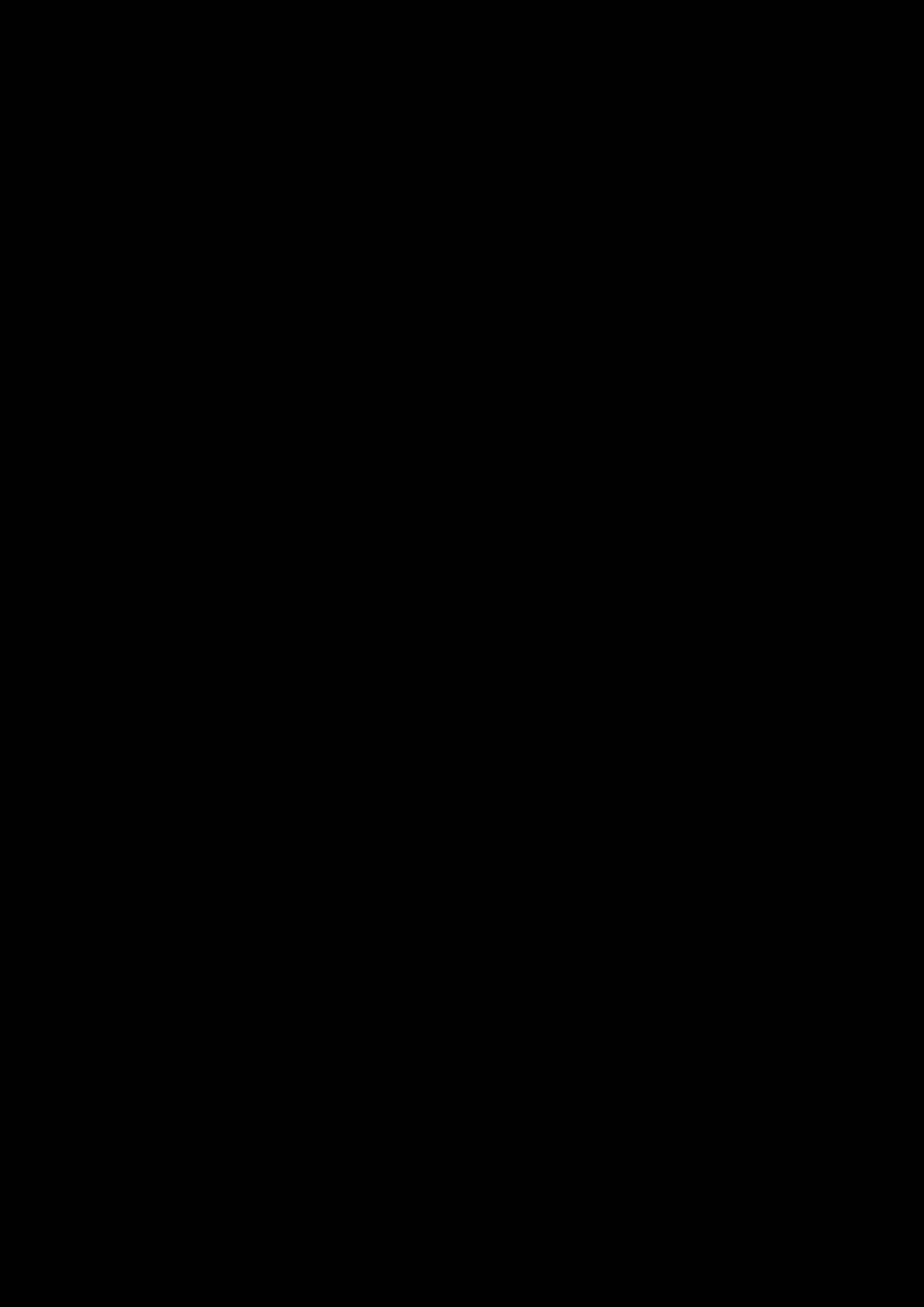 |